Our previous vehicle only had two thrusters in the rear, which meant we didn’t have strafing or station keeping abilities. Thus, for Fish ‘N Ships, it was very important to us to use an x-drive configuration (two thrusters in the front and two thrusters in the back of the hulls). This allowed our new vehicle to strafe and station-keep with ease. However, we didn’t know the best angle to mount the thrusters, and we wanted to keep it adjustable so that we can test out the best configuration. Therefore, we designed an attachment on the bottom of the hulls that had holes in 22.5 degree increments, to allow us to easily attach the thrusters in different positions.
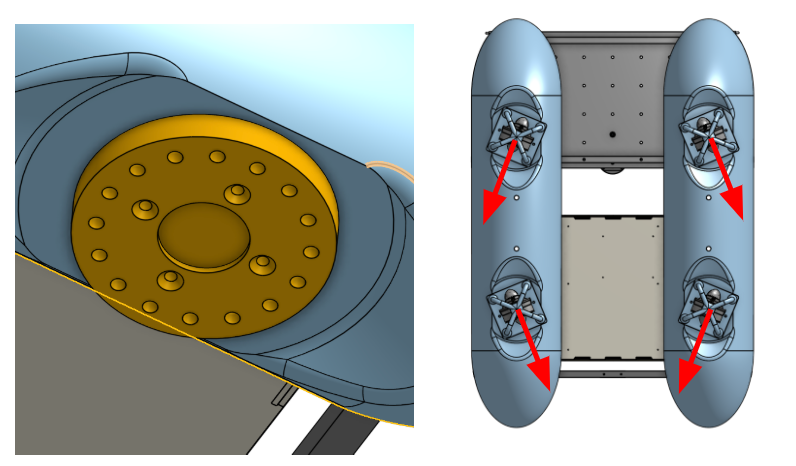
Fig 1. The left image shows the marine plywood we attached to our hulls to allow 22.5 degree rotations of our thrusters. The right image shows the x-drive configuration.
Another design consideration we had in mind was to add some sort of protection to the thrusters. In the past, we could not set the vehicle down without propping it on a platform since the thrusters protruded from the hulls. This made it difficult to transport and test the boat. Therefore, our team decided to add some thruster cages to allow us to set the boat on the ground.
In our initial design, we mounted two U-bolts for each thruster, but we quickly realized that the U-bolts were quite heavy, contributing to 10% of the overall vehicle weight. Therefore, we considered different materials and geometry to reduce the weight. For material, we decided to SLA 3D print using Formlabs Tough 2K resin. As for geometry, two different designs were considered. The first design weighed a total of 2.4 lbs, and the second design has a total weight of 4.15 lbs. We ended up choosing the first design in consideration of weight restraints. However, we wanted to make sure that the first design can still withstand a reasonable amount of force, so we verified with FEA performed on OnShape and physical tests. The results showed that each cage could support over 150lbs, which is more than sufficient for our design, and now, the cages only contribute to 4% of the total weight.
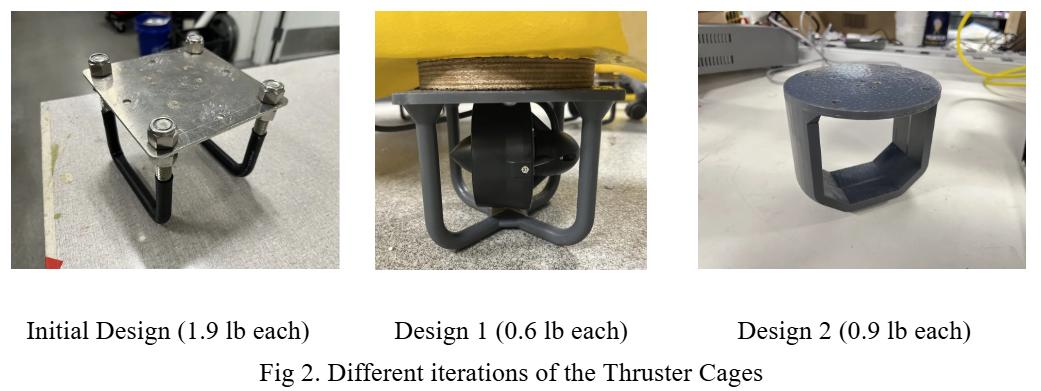